Chapter 296-874, WAC
WAC 296-874-100: Scope
This chapter applies to suspended and supported scaffolds, including their supporting structures and anchorage points.
Exemption: This chapter doesn’t apply to:
-
- Manually propelled elevating work platforms
- Self-propelled elevating work platforms
- Boom-supported elevating work platforms
- Aerial lift
- Crane or derrick suspended personnel platforms
- Personnel platforms supported by powered industrial trucks (PITs).
Reference: Additional requirements for the following types of platforms are found in the General Safety and Health Standards, Chapter 296-24 WAC. Go to the following sections:
-
- For elevating work platforms and aerial lifts, go to Elevating Work Platforms, WAC 296-24-875
- For crane or derrick suspended personnel platforms, go to WAC 296-24-23533
- For personnel platforms supported by powered industrial trucks (PITs), go to WAC 296- 863.
Definition:
-
- A scaffold is a temporary elevated platform, including its supporting structure and anchorage points, used for supporting employees or materials.
- A suspended scaffold is one or more platforms suspended from an overhead structure by ropes or other nonrigid means.
- A supported scaffold is one or more platforms supported by rigid means such as outrigger beams, brackets, poles, legs, uprights, posts, or frames.
WAC 296-874-200: General Requirements for Scaffolds
Make sure scaffolds are properly designed and constructed
-
- Make sure scaffolds are: Designed by a qualified person and Constructed according to that design.
- Prohibit the use of shore and lean-to scaffoldsDefinition: A qualified person is one who has demonstrated the ability to solve problems related to the subject matter, work, or project. This can be done by having either:
- A recognized degree, certificate, or professional standing; or
- Extensive knowledge, training, and experience.
Make sure scaffolds are erected, moved, altered, or dismantled by appropriate persons
-
- Make sure scaffolds are erected, moved, altered, or dismantled only when the work is:
- Supervised and directed by a competent person qualified in scaffold erections, moving, dismantling or alteration; and
- Done by experienced and trained employees selected by the competent person.
Definition: A competent person is someone who is capable of identifying existing and predictable hazards in the surroundings or working conditions which are unsanitary, hazardous, or dangerous to employees and has the authority to take prompt corrective measures to eliminate them.
- Make sure scaffolds are erected, moved, altered, or dismantled only when the work is:
Maintain structural integrity when intermixing scaffold components
-
- Make sure intermixed scaffold components: Fit together without force and maintain the scaffold’s structural integrity.
- Make sure a qualified person determines that modifying components in order to intermix them will result in a structurally sound scaffold.
- Make sure scaffold components made of different metals aren’t used together.Exemption: Different types of metals may be used together if a competent person determines that galvanic action won’t reduce the strength of any component to less than the minimum strength required.
Reference: The minimum strength requirements are found in the following sections:- Suspended Scaffolds, WAC 296-874-30002
- Supported Scaffolds, WAC 296-874-40002.
Make sure platforms are properly planked or decked Fully plank or deck each platform between the front uprights and the guardrail supports on all working levels of a scaffold so that there’s no more than one inch (2.5 cm):
-
- Between adjacent units, and between the platform and the uprights. Exemption: There may be more than one inch between platform units if all of the following are met:
- You can demonstrate that a wider space is necessary, such as to fit around uprights when side brackets are used to extend the platform width
- The platform is planked or decked as fully as possible
- The open space between the platform and the guardrail supports is 9-1/2 inches (24.1 cm) or less.
- Between adjacent units, and between the platform and the uprights. Exemption: There may be more than one inch between platform units if all of the following are met:
-
- Platforms used solely as walkways or only by employees erecting or dismantling scaffolds, don’t have to be fully decked or planked if:
- The planking provided makes for safe working conditions, and
- Employees on those platforms are protected from falling.
- Platforms used solely as walkways or only by employees erecting or dismantling scaffolds, don’t have to be fully decked or planked if:
Fall protection requirements for employees | Are located in the following chapters | In the following sections |
---|---|---|
On walkways within scaffolds | Chapter 296-874, WAC Scaffolds | WAC 296-874-20030 |
Erecting or dismantling supported scaffolds | Chapter 296-874, WAC Scaffolds | WAC 296-874-40008 |
Erecting or dismantling suspended scaffolds in general industry | Chapter 296-24, WAC General Safety and Health Standards | Part J-1, Working Surfaces, Guarding Floors and Wall Openings, Ladders and Part J-3, Powered Platforms |
Erecting or dismantling suspended scaffolds in construction work | Chapter 296-155, WAC Safety Standards for Construction Work | Part C-1, Fall Restraint and Fall Arrest and Part K, Floor Openings, Wall Openings, and Stairways |
Make sure wood platforms aren’t covered with an opaque finish
Exemption: Platform edges may be covered or marked for identification.
Note: Platforms may be coated periodically with wood preservatives, fire-retardant finishes, or slip-resistant finishes if the coating doesn’t obscure the top or bottom wood surfaces.
WAC 296-874-20010: Make sure platforms meet minimum width requirements
Make sure scaffold platforms meet the minimum width requirements of Table 1.
Types of scaffold | Minimum platform width required |
---|---|
Ladder jack scaffold Pump jack scaffold Roof bracket scaffold Top plate bracket scaffold | 12 inches (20 cm) |
Boatswain's chair | No minimum width |
All other scaffolds | 18 inches (46 cm) Exemption: Platforms and walkways may be less than 18 inches (46 cm) wide if all of the following are met: You can demonstrate that the area is so narrow that the platform or walkway can't be at least 18 inches (46 cm) wide The platform or walkway is as wide as feasible Employees on those platforms or walkways are protected from falling by using guardrails or personal fall arrest systems |
Meet these requirements when using shorter platforms to create a longer platform
-
- When platforms are overlapped to create a longer platform, that:
- The overlap is over a support; and
- The platforms are either:
- When platforms are overlapped to create a longer platform, that:
-
-
- Overlapped by at least 12 inches (30 cm); or
- Are nailed together or otherwise prevented from moving.
-
-
- When platforms are butted together to create a longer platform, that each abutted platform end rests on a separate support surface.
Note:
-
- Platforms may butt together on a common support member if the member is designed to support abutting platforms, such as either:
- A “T” section; or
- Hook-on platforms designed to rest on common supports
- Platforms may butt together on a common support member if the member is designed to support abutting platforms, such as either:
WAC 296-874-20014: Lay platform planks properly when the platform changes direction
Do the following whenever platforms overlap to change direction: First lay the platform that rests on a barer at an angle other than a right angle then lay the platform that’s perpendicular to the bearer.
WAC 296-874-20016: Stabilize the ends of platforms
-
- Make sure each end of a platform:
- Is cleated or restrained by hooks or equivalent means; or
- Extends over the centerline of its support at least 6 inches (15 cm).
- Make sure the cantilevered portion of a platform meets at least one of the following:
- Is designed and installed to support employees or material without tipping
- Has guardrails which block employee access to the cantilevered end
- Extends over its support not more than:
- 12 inches (30 cm) if the platform length is 10 feet or less, or
- 18 inches (46 cm) if the platform length is greater than 10 feet. Note: The cantilevered portion of a platform is the portion that isn’t supported on one end.
- Make sure each end of a platform:
WAC 296-874-20018: Keep platform sag within acceptable limits
Make sure a loaded platform doesn’t sag more than 1/60 of the span.
Provide safe access to scaffolds
-
- Provide scaffold platforms more than 2 feet (0.6 m) above or below a point of access with at least one of the following means of access:
- Portable, hook-on, or attachable ladder
- Stairway-type ladder
- Ladder stand
- Stair tower (scaffold stairway or tower)
- Ramp
- Walkway
- Integral prefabricated scaffold access
- Direct access from another scaffold, structure, personnel hoist, or similar surface.
* Crossbraces cannot be used as a means of access.
Reference: For requirements about integral prefabricated scaffold access, go to WAC 296-874-40020.
- Provide scaffold platforms more than 2 feet (0.6 m) above or below a point of access with at least one of the following means of access:
Portable, hook-on, and attachable ladders must meet these requirements:
-
- Position portable, hook-on, and attachable ladders so they don’t tip the scaffold.
- Make sure hook-on and attachable ladders meet all of the following:
- Specifically designed and used for that type of scaffold
- Have rungs that are:
- Uniformly spaced
- Not more than 16-3/4 inches apart
- At least 11-1/2 inches (29 cm) long
- Lined up vertically between rest platforms.
- Position the bottom rung not more than 24 inches (61 cm) above the scaffold supporting level.
- Have rest platforms at vertical intervals not greater than 24 feet (7.3m) on supported scaffolds.
Stairway-type ladders must meet these requirements:
-
- Make sure stairway-type ladders meet all of the following:
- Position the bottom step not more than 24 inches (61 cm) above the scaffold supporting level
- Have rest platforms not more than 12 feet (3.7 m) apart vertically
- Have slip-resistant surfaces on treads and landings
- Have steps that:
- Are at least 16 inches (41 cm) wide; and
- Line-up vertically between rest platforms.
- Make sure mobile ladder stands have steps that are at least 11-1/2 inches (30 cm) wide.
Definition: A ladder stand is a mobile, fixed-size, self-supporting ladder consisting of a wide flat tread ladder in the form of stairs.
- Make sure stairway-type ladders meet all of the following:
Stair towers must meet these requirements:
-
- Make sure stair towers (scaffold stairways or towers) meet all of the following:
- Are positioned so the bottom step isn’t more than 24 inches (61 cm) above the scaffold supporting level
- Are at least 18 inches (45.7 cm) wide between stair rails
- Have slip-resistant surfaces on treads and landings
- Are installed at an angle of 40 to 60 degrees from the horizontal.
- Provide a landing platform at least 18 inches (45.7 cm) wide by 18 inches (45.7 cm) long at each level.
- Provide guardrails on the open sides and ends of each landing.
Reference: For requirements about guardrails, go to WAC 296-874-20064.
- Make sure stair towers (scaffold stairways or towers) meet all of the following:
Steps must meet all of the following requirements:
-
- Line-up vertically between rest platforms
- Have uniform tread depth, within 1/4 inch (0.6 cm), for each flight of stairs
- Have uniform riser height, within 1/4 inch (0.6 cm), for each flight of stairs.
Note: Riser height may have larger variations at the top step and bottom step of the entire stair system, but not at the top and bottom steps within each flight of stairs.
Stair rails and handrails must meet these requirements:
-
- Provide a stair rail that meets all of the following on each side of a scaffold stairway:
- Has a toprail and midrail
- Has a toprail that can serve as a handrail if a separate handrail isn’t provided
- Is at least 28 inches (71 cm) but not more than 37 inches (94 cm) high.
Note: Stair rail height is measured from the upper surface of the stair rail to the surface of the tread, in line with the face of the riser at the forward edge of the tread.
- Make sure stair rail systems and handrails have:
- A surface that prevents employees from:
- Being injured by punctures or lacerations; or snagging their clothing.
- Ends that don’t create a projection hazard.
- A surface that prevents employees from:
- Make sure handrails, and top rails that are used as handrails:
- Provide an adequate handhold for employees to grasp to avoid falling; and
- Are at least 3 inches (7.6 cm) from other objects.
- Provide a stair rail that meets all of the following on each side of a scaffold stairway:
Ramps and walkways used to access scaffolds must meet these requirements:
-
- Make sure ramps and walkways aren’t inclined at a slope steeper than one vertical in 3 horizontal (1:3 or 20 degrees from the horizontal).
- Make sure ramps and walkways that are inclined at a slope steeper than one vertical in 8 horizontal (1:8) have cleats to provide footing which are:
- Securely fastened to the planks; and
- Spaced not more than 14 inches (35 cm) apart.
Reference: Ramps and walkways that are 4 feet (1.2 m) or more above a lower level need to have a guardrail system. Those requirements are found in other chapters.
-
- For general industry activities, go to: Working Surfaces, Guarding Floors and Wall Openings, Ladders, Part J-1, in the General Safety and Health Standards, Chapter 296-24 WAC
- For construction activities, go to: Floor Openings, Wall Openings, and Stairways, Part K, in the Safety Standards for Construction Work, Chapter 296-155 WAC.
WAC 296-874-20032: Surfaces used to access scaffolds are close enough to use safely.
Surface used to provide access to or from a scaffold isn’t further from the scaffold than:
-
- 14 inches (36 cm) horizontally
- 24 inches (61 cm) vertically.
WAC 296-874-20034: Inspect scaffolds and scaffold components.
Make sure scaffolds and scaffold components are inspected for visible defects by a competent person:
-
- Before each work shift; and
- After anything occurs that could affect the scaffold’s structural integrity
WAC 296-874-20036: Damaged or weakened scaffolds must meet minimum strength requirements.
Make sure any scaffold or scaffold component that’s been damaged or weakened so that it no longer meets the minimum strength requirements of this chapter, is immediately either:
-
- Repaired, replaced, or braced to meet the minimum strength requirements; or
- Removed from service until repaired.
Reference: For information on minimum strength requirements for suspended and supported scaffolds, go to the following sections within this chapter:- Make sure suspended scaffolds and suspended components meet these strength requirements, WAC 296-874-30002
- Make sure supported scaffolds and supported components meet these strength requirements, WAC 296-874-40002.
WAC 296-874-20038: Scaffolds are properly loaded
Load scaffolds as specified in the:
-
- Manufacturer’s instructions; or
- Design of the qualified person.
- Make sure scaffolds and scaffold components don’t exceed their maximum intended load or rated load, whichever is less.
WAC 296-874-20040: Protect employees when moving scaffolds.
Make sure scaffolds aren’t moved horizontally while employees are on them.
Exemption: A scaffold may be moved horizontally with employees on it if the scaffold:
-
- Has been specifically designed for such movement by a registered professional engineer; or
- Is a mobile scaffold that meets the requirements of the section, Meet these requirements when moving mobile scaffolds, WAC 296-874-40012.
WAC 296-874-20042: Increase employee working level height on scaffolds safely
Make sure makeshift devices, such as boxes and barrels, aren’t used on scaffold platforms to increase the working level height for employees.
-
- Meet all of the following when using stilts on scaffolds:
- Use stilts only on large area scaffolds
- Increase the height of a guardrail system used for fall protection by an amount equal to the height of the stilts being used
- Meet all of the following when using stilts on scaffolds:
-
- Make sure scaffold platforms where stilts are used are flat and free of:
- Pits, holes, and obstructions such as debris; and
- Other tripping or falling hazards.
- Make sure stilts are:
- Properly maintained; and
- The original equipment isn’t altered without the manufacturer’s approval
- Meet all of the following when using ladders on scaffolds:
- Use ladders only on large area scaffolds
- Secure the platform units to the scaffold to prevent movement
- Secure the scaffold against the sideways thrust exerted by the ladder if the ladder is placed against a structure that’s not part of the scaffold
- Make sure the ladder legs are:
- Secured to prevent them from slipping or being pushed off the platform; and
- On the same scaffold platform, or use other means, to stabilize the ladder against uneven platform deflection.
- Make sure scaffold platforms where stilts are used are flat and free of:
WAC 296-874-20044: Control loads being hoisted near scaffolds
Use a tag line or equivalent measures to control loads being hoisted onto or near a scaffold if the load could swing and contact the scaffold.
WAC 296-874-20046: Protect employees from energized power lines
Make sure scaffolds are erected, moved, altered, or dismantled so that they, and any conductive material handled on them, are kept at least as far from exposed and energized power lines as shown in Table 2, Minimum Separation Distance from Energized Power Lines.
Voltage | Minimum Separation Distance |
---|---|
Less than 300 volts (insulated lines) | 3 feet (0.9 m) |
Less than 300 volts (uninsulated lines) | 10 feet (3.1 m) |
300 volts to 50 kv | 10 feet (3.1 m) |
More than 50 kv | 10 feet (3.1 m) + 0.4 inches (1.0 cm) for each 1 kv over 50 kv Note: You may use alternative minimum separation distance of 2 times the length of the line insulator, but never less than 10 feet (3.1 m). |
Exemption: Scaffolds and conductive materials handled on scaffolds may be closer to power lines than the minimum separation distance specified in Table 2 if all of the following are met:
-
- Less clearance is necessary to do the work
- The utility company or electrical system operator has been notified of the need to work closer to the power lines
- The utility company or electrical system operator has done at least one of the following:
- De-energized the lines
- Relocated the lines to meet the minimum separation distance requirement
- Installed protective coverings over the lines to prevent accidental contact
WAC 296-874-20048: Protect employees from weather hazards
Prohibit work on or from scaffolds during storms or high winds unless both of the following are met:
-
- A competent person has determined that it’s safe for employees to be on the scaffold Employees are protected by either:
- A personal fall arrest system; or
- Windscreens.
- Make sure wind screens aren’t used unless the scaffold is secured against the anticipated wind forces.
- A competent person has determined that it’s safe for employees to be on the scaffold Employees are protected by either:
WAC 296-874-20050: Protect employees from slipping and tripping hazards.
-
- Make sure debris doesn’t accumulate on platforms.
- Prohibit employees from working on scaffolds covered with snow, ice, or other slippery material.
Exemption: Employees may be on scaffolds as necessary to remove the slipping hazard.
WAC 296-874-20052: Provide fall protection for employees on scaffolds.
Protect each employee on a scaffold more than 10 ft. (3.1 m) above a lower level, from falling to the lower level, by providing either:
-
- A personal fall arrest system; or
- Guardrails.
Make sure employees erecting the scaffold install the guardrail system, if required, before the scaffold is used by any other employees.
Fall protection requirements for employees | Are located in the following chapters | In the following sections |
---|---|---|
On walkways within scaffolds | Chapter 296-874, WAC Scaffolds | WAC 296-874-20030 |
Erecting or dismantling supported scaffolds | Chapter 296-874, WAC Scaffolds | WAC 296-874-40008 |
Erecting or dismantling suspended scaffolds in general industry | Chapter 296-24, WAC General Safety and Health Standards | Part J-1, Working Surfaces, Guarding Floors and Wall Openings, Ladders and Part J-3, Powered Platforms |
Erecting or dismantling suspended scaffolds in construction work | Chapter 296-155, WAC Safety Standards for Construction Work | Part C-1, Fall Restraint and Fall Arrest and Part K, Floor Openings, Wall Openings, and Stairways |
WAC 296-874-20054: Provide fall protection if a scaffold is too far from the work face.
Provide a guardrail system along the front edge of the platform, or have employees use a personal fall arrest system, if the distance from the front edge of the platform to the work face is greater than:
-
- 18 inches (46 cm) for scaffolds used for plastering and lathing operations.
- 14 inches (36 cm) for all other scaffolds
WAC 296-874-20056: Provide specific fall protection for specific types of scaffolds.
Use a personal fall arrest system to protect employees on the following scaffolds:
-
- Boatswain’s chair
- Catenary scaffold
- Float scaffold
- Ladder jack scaffold
- Needle beam scaffold.
Use a personal fall arrest system and a guardrail system to protect employees on:
-
- Single-point adjustable suspension scaffolds; and
- Two-point adjustable suspension scaffolds.
Protect employees working on a self-contained adjustable scaffold that has the platform:
-
- Supported by the frame structure, using a guardrail system with a minimum 200 lb. toprail capacity.
- Suspended by ropes, using:
- A guard rail system with a minimum 200 lb. toprail capacity; and
- A personal fall arrest system.
- Protect employees on walkways located within a scaffold by using a guardrail system that meets all of the following:
- Has a minimum 200 lb. toprail capacity
- Is installed within 9-1/2 inches (24.1 cm) of the walkway
- Is installed along at least one side of the walkway.
WAC 296-874-20058: Personal fall arrest systems must meet these requirements:
Make sure personal fall arrest systems used on scaffolds for general industry activities, meet the requirements of Personal Fall Arrest System, Appendix C, Part 1, WAC 296-24-88050, in Powered Platforms, Part J-3, found in General Safety and Health Standards, Chapter 296-24, WAC.
Make sure personal fall arrest systems are attached by a lanyard to one of the following:
-
- Vertical lifeline
- Horizontal lifeline
- Appropriate structural member of the scaffold
Reference: Requirements for personal fall arrest systems used on scaffolds for construction activities are in Fall Restraint and Fall Arrest, Part C-1, found in Safety Standards for Construction Work, Chapter 296-155, WAC.
WAC 296-874-20060: Vertical lifelines used with personal fall arrest systems must meet these requirements:
Make sure vertical lifelines are all of the following:
-
- Fastened to a fixed, safe point of anchorage
- Independent of the scaffold
- Protected from sharp edges and abrasion.
- Note: Safe points of anchorage include structural members of buildings, but do not include:
- Standpipes, vents, or other piping systems
- Electrical conduit
- Outrigger beams
- Counterweights
Make sure vertical lifelines, independent support lines, and suspension ropes are not attached to any of the following:
-
- Each other
- The same point of anchorage
- The same point on the scaffold.
Make sure vertical lifelines, independent support lines, and suspension ropes don’t use the same point of anchorage.
Make sure independent support lines and suspension ropes aren’t attached to a personal fall arrest system.
Make sure vertical lifelines aren’t used with single-point or two-point adjustable suspension scaffolds that have overhead components such as overhead protection or additional platform levels.
WAC 296-874-20062: Horizontal lifelines used with personal fall arrest systems must meet these requirements:
Equip single-point or two-point adjustable suspension scaffolds that use horizontal lifelines or structural members of the scaffold for fall protection with both of the following:
-
- Additional independent support lines that are equal in number and equivalent in strength to the suspension ropes
- Automatic locking devices capable of stopping the scaffold from falling if one or both of the suspension ropes fail.
Make sure horizontal lifelines are secured to either:
-
- Two or more structural members of the scaffold; or
- Looped around both the suspension ropes and independent support lines above the hoist and brake attached to the end of the scaffold.
Make sure independent support lines and suspension ropes are not:
-
- Attached to each other or the same point on the scaffold
- Attached to or use the same point of anchorage.
Make sure independent support lines and suspension ropes aren’t attached to either:
-
- A personal fall arrest system; or
- The same point on the scaffold as a personal fall arrest system.
Make sure, if a horizontal lifeline is used where it may become a vertical lifeline, that the device used to connect a lanyard to the horizontal lifeline is capable of locking in both directions on the lifeline.
WAC 296-874-20064: Guardrail systems must meet these requirements:
Make sure guardrails, if required, are installed along all open sides and ends of platforms. Exemption: For employees doing overhand bricklaying operations from a supported scaffold, a guardrail isn’t required on the side next to the wall. Definition: Overhand bricklaying is the process of laying bricks and masonry units so that the surface of the wall is on the opposite side of the wall from the mason, requiring the mason to lean over the wall to complete the work. It includes mason tending and electrical installation incorporated into the brick wall.
Make sure the height of the toprail top edge, or the equivalent member, of supported scaffolds is:
-
- At least 36 inches (0.9 m) and not more than 45 inches (1.2 m) above the platform surface for scaffolds manufactured or first placed in service before January 1, 2000.
- At least 38 inches (0.97 m) and not more than 45 inches (1.2 m) above the platform surface for scaffolds manufactured or first placed in service after January 1, 2000.
Make sure the height of the toprail top edge, or the equivalent member, of suspended scaffolds that require guardrails and personal fall arrest systems, is at least 36 inches (0.9 m) and not more than 45 inches (1.2 m) above the platform surface. Exemption: When conditions warrant, the height of the top edge of the toprail may be greater than 45 inches if the guardrail system meets all other criteria of this chapter.
Make sure the top edge of the toprail doesn’t drop below the required height when the minimum load, shown in Table 3, Minimum Toprail and Midrail Strength Requirements, is used.
Each toprail and midrail, or equivalent member, of a guardrail system must be able to withstand, without failure, the force shown in Table 3, Minimum Toprail and Midrail Strength Requirements, when the force is applied as follows:
-
- To the toprail in a downward or horizontal direction at any point along its top edge
- To the midrail in a downward or horizontal direction at any point.
Note: Midrail includes screens, mesh, intermediate vertical members, solid panels, and equivalent structural members of the guardrail system.
Type of Scaffold | Toprail Capacity | Midrail Capacity |
---|---|---|
Single-point adjustable suspension scaffolds Two-point adjustable suspension scaffolds | 100 lbs. (445 n) | 75 lbs. (333 n) |
All other scaffolds Walkways within a scaffold | 200 lbs. (890 n) | 150 lbs. (666 n) |
Install midrails, screens, mesh, intermediate vertical members, solid panels, or equivalent structural members as follows:
-
- Midrails at a height approximately midway between the top edge of the guardrail system and the platform surface
- Screens and mesh:
- From the top edge of the guardrail system to the scaffold platform; and
- Along the entire opening between the supports
- Intermediate members, such as balusters or additional rails, not more than 19 inches (48 cm) apart.
- Make sure steel or plastic banding isn’t used as a toprail or midrail.
-
- Have a competent person inspect manila rope and plastic or other synthetic rope that’s used as a toprail or midrail as frequently as necessary to make sure it continues to meet the strength requirements for a toprail or midrail.
Note: Crossbraces may be used as a toprail or midrail in a guardrail system if they meet the following requirements:
- Have a competent person inspect manila rope and plastic or other synthetic rope that’s used as a toprail or midrail as frequently as necessary to make sure it continues to meet the strength requirements for a toprail or midrail.
-
-
-
- The crossing point of the 2 braces is between:
- 20 inches and 30 inches above the work platform when used as a midrail
- 38 inches and 48 inches above the work platform when used as a toprail
- The end points at each upright aren’t more than 48 inches apart.
- Make sure guardrails have a surface that prevents:
- Puncture and laceration injuries; and
- Snagging clothing.
- Make sure any rail extending beyond the post of a guardrail doesn’t create a projection hazard.
- The crossing point of the 2 braces is between:
-
-
WAC 296-874-20066: Provide falling object protection.
Protect employees from being struck by tools, materials, or equipment falling from a scaffold by doing one or more of the following:
-
- Use a barricade to keep employees out of the area where falling objects could be a hazard
- Install a toeboard along the edge of the platform anywhere an object could fall on an employee below
- Install paneling or screening that covers from the top of the guardrail to the toeboard or platform anywhere the toeboard is not high enough to keep objects from falling off the platform
- Install a guardrail system with openings small enough to keep potential falling objects from passing through
- Erect a canopy structure, debris net, or catch platform over employees that does all of the following:
- Will contain or deflect falling objects
- Is strong enough to withstand the impact forces
- Is installed between the falling object hazard and the employees.
- Make sure potential falling objects that are too large or heavy to be contained or deflected by the falling object protection you’re using, are:
- Moved away from the edge of the surface they could fall from; and
- Secured, as necessary, to prevent falling
Reference: Hardhats and possibly other personal protective equipment has to be used to protect employees exposed to overhead hazards.
* Those requirements are found in the Safety and Health Core Rules, Chapter 296-800 WAC. Go to the section titled Personal Protective Equipment (PPE), WAC 296-800- 160.
WAC 296-874-20068: Provide additional support lines on suspended scaffolds using a canopy for falling object protection.
Equip suspended scaffolds, that use a canopy for falling object protection, with additional independent support lines that meet all of the following:
-
- Have the same number of support lines as there are suspension ropes
- Are equivalent in strength to the suspension ropes
- Aren’t attached to the same point of anchorage as the suspension ropes.
WAC 296-874-20070: Toeboards must meet these requirements:
Make sure toe boards, when used, are:
-
- At least 3-1/2 inches (9 cm) high from the top edge of the toe board to the platform
- Securely fastened along the outer edge of the platform
- Installed for enough distance along the platform to protect employees below
- Installed so the gap between the bottom of the toe board and the platform is 1/4 inch (0.7 cm) or less
- Solid or with openings that are one inch (2.5 cm) or less in the largest dimension
- Able to withstand, without failing, a force of at least 50 lbs. (222 n) applied in a downward or horizontal direction anywhere along the toe board.
Exemption: On float (ship) scaffolds, an edging of 3/4 x 1-1/2 inch (2×4 cm) wood or the equivalent may be used instead of a toe board.
WAC 296-874-20072: Train employees who work on a scaffold.
Have a qualified person train each employee who works on a scaffold to:
-
- Recognize the hazards associated with the type of scaffold they are using; and
- Understand the procedures to control or minimize the hazards.
- Include the following subjects in your training:
- Hazards in the work area and how to deal with them, including:
- Electrical hazards
- Fall hazards
- Falling object hazards
- How to erect, maintain, and disassemble the fall protection and falling object protection systems being used
- How to:
- Use the scaffold
- Handle materials on the scaffold
- The load-carrying capacity and maximum intended load of the scaffold
- Any other requirements of this chapter that apply.
- Hazards in the work area and how to deal with them, including:
WAC 296-874-20074: Train employees who erect, dismantle, operate or maintain scaffolds
Have a competent person train each employee who erects, disassembles moves, operates, repairs, maintains, or inspects scaffolds to recognize any hazards associated with the work.
Make sure the training includes at least the following subjects:
-
- Hazards in the work area and how to deal with them
- The correct procedures for erecting, disassembling, moving, operating, repairing, inspecting, and maintaining the type of scaffold being used
- The design criteria, maximum intended load-carrying capacity and intended use of the scaffold
- Any other requirements of this chapter that apply.
WAC 296-874-20076: Retrain employees when necessary.
Retrain employees to reestablish proficiency if you believe they lack the skill or understanding to safely erect, use, or dismantle a scaffold.
Retraining is required in at least the following situations:
-
- An employee’s work involving scaffolds is inadequate and indicates they lack the necessary proficiency
- A change in any of the following that presents a hazard the employee hasn’t been trained for:
- Worksite
- Type of scaffold
- Fall protection
- Falling object protection
- Other equipment
WAC 296-874-30002: Suspended scaffolds and scaffold components must meet these strength requirements:
Meet the following strength requirements:
-
- Suspended scaffolds must support, without failure, the total of their own weight plus 4 times the maximum intended load
- Suspended scaffold components must meet the requirements contained in Table 4, Suspended Scaffold Strength Requirements.
- Surfaces that support scaffold support devices must withstand 4 times the rated load of the hoist:
Note: Scaffold support devices include outrigger beams, cornice hooks, parapet clamps, and similar devices.
These scaffold components | Must meet these strength requirements |
---|---|
| Support 6 times the rated load of the hoist |
| Resist 4 times the tipping moment with the scaffold operating at the rated load of the hoist |
| Support 6 times the maximum intended load applied or transmitted to the rope |
| Support its own weight plus 4 times the maximum intended load |
WAC 296-874-30004: Suspended scaffold outrigger beams must meet these requirements:
Make sure outrigger beams are made of structural metal or equivalent strength material.
Stabilize the inboard ends of outrigger beams by using either:
-
- Bolts or other direct connections to the floor or roof deck; or
- Counterweights and tiebacks.
Exemption: Masons’ multi-point adjustable scaffold outrigger beams can not be stabilized by counterweights.
Make sure, before the scaffold is used, that a competent person:
-
- Evaluates the direct connections, and
- Confirms that the supporting surfaces can support the loads placed on them.
Make sure suspended scaffold outrigger beams are all of the following:
-
- Restrained to prevent moving
- Provided with stop bolts or shackles at both ends
- Securely fastened together with the flanges turned out when channel iron beams are used in place of I-beams
- Set and maintained with the web in a vertical position
- Placed so the suspension rope is centered over the stirrup.
- Place outrigger beams at a right angle (perpendicular) to their bearing support.
Exemption: Outrigger beams can be placed at other than a right angle (perpendicular) if:- You can demonstrate that immovable obstructions make it impossible to place the beams at a right angle (perpendicular) to their bearing support, and
- Opposing angle tiebacks are used.
Note: The angle between the outrigger beam and the bearing support is usually the same as the angle between the outrigger beam and the face of the building or structure.
WAC 296-874-30006: Counterweights must be safe and used properly.
Make sure counterweights:
-
- Are made of material that can’t flow; and
- Have been specifically designed to be used as counterweights.
Note: The following can’t be used as counterweights:- Sand, gravel and similar materials that can be easily dislocated; and
- Construction material such as masonry units and roofing felt.
- Secure counterweights to outrigger beams by mechanical means to prevent them from being accidentally detached.
- Leave counterweights attached to the outrigger beams until after the scaffold has been disassembled
WAC 296-874-30008: Make sure tiebacks meet these requirements.
Make sure tiebacks are equivalent in strength to the suspension ropes.
Make sure tiebacks are secured to a structurally sound anchorage on the building or structure and installed:
-
- At a right angle (perpendicular) to the face of the building or structure; or
- As opposing angle tiebacks.
WAC 296-874-30010: Suspended scaffold support devices must meet these requirements:
Make sure suspended scaffold support devices, such as cornice hooks, roof hooks, roof irons, parapet clamps, or similar devices, are:
-
- Made of steel, wrought iron, or other material of equivalent strength
- Supported by bearing blocks
- Prevented from moving by using tiebacks.
Reference: For outrigger beam requirements, go to WAC 296-874-30004. For tieback requirements, go to WAC 296-874-30008.
WAC 296-874-30012: Scaffold hoists must meet these requirements:
Make sure the stall load of any scaffold hoist is not more than 3 times its rated load.
Make sure the design of scaffold hoists has been tested by an independent nationally recognized testing laboratory.
Make sure scaffold hoists have both a:
-
-
- Normal operating brake; and
- Braking device or locking pawl which automatically engages when the hoist has an uncontrolled:
- Instantaneous change in momentum; or
- An accelerated overspeed.
-
Prohibit use of gasoline-powered hoists on suspended scaffolds.
Enclose the gears and brakes of power-operated hoists used on suspended scaffolds.
Make sure manually-operated hoists need a positive crank force to descend.
WAC 296-874-30014: Scaffold hoists must retain enough suspension rope.
Make sure the suspension rope on winding drum hoists is long enough to wrap around the drum at least 4 times when the scaffold is at its lowest point of travel.
Make sure the suspension rope on hoists that do not use a winding drum:
-
- Is long enough to allow the scaffold to be lowered to the level below without the rope end passing through the hoist; or
- Has the rope end configured, or uses other means, to prevent it from passing through the hoist.
WAC 296-874-30016: Wire rope must be in good condition.
Make sure a competent person inspects each rope for defects:
-
- Before each work shift; and
- After anything happens that could affect the rope’s integrity.
- Replace a rope if it has any of the following:
- Physical damage which impairs the function and strength of the rope
- Kinks that could impair the tracking or wrapping of the rope around a drum or sheave
- 6 randomly distributed broken wires in one rope lay
- 3 broken wires in one strand of one rope lay
- Loss of more than 1/3 of the original diameter of the outside wires caused by abrasion, corrosion, scrubbing, flattening or peening
- Heat damage caused by a torch
- Any damage caused by contact with electrical wires
- Evidence that the secondary brake has been activated during an overspeed condition and has engaged the suspension rope.
- Prohibit the use of repaired wire rope as suspension rope.
WAC 296-874-30018: Wire suspension rope connections must meet these requirements:
Only use eye splice thimbles connected with shackles or cover plates and bolts to join wire suspension ropes together.
Make sure the load ends of wire suspension ropes are:
-
- Equipped with proper size thimbles
- Secured by eye splicing or an equivalent means.
Make sure all swaged attachments or spliced eyes on wire suspension rope has been made by either:
-
- The wire rope manufacturer; or
- A qualified person.
WAC 296-874-30020: Wire rope clips must be used properly
Make sure, if wire rope clips are used on suspended scaffolds, such as on the suspension ropes or support lines, that:
-
- A minimum of 3 clips are installed
- The distance between clips is at least 6 rope diameters
- Clips are installed according to the manufacturer’s recommendations.
- Retighten the clips to the manufacturer’s recommendations after the initial loading.
- Inspect the clips and retighten them to the manufacturer’s recommendations at the start of each work shift.
- Make sure U-bolt clips aren’t used at the point of suspension for any scaffold hoist.
- Make sure, if U-bolt clips are used, that:
- The U-bolt is placed over the dead end of the rope; and
- The saddle is placed over the live end of the rope.
WAC 296-874-30022: Prevent swaying of two-point and multi-point suspension scaffolds.
Tie or use other means to keep two-point and multi-point suspension scaffolds from swaying, if an evaluation by a competent person determines it is necessary.
Note: Window cleaners’ anchors cannot be used to secure scaffolds since they aren’t designed to withstand the load.
WAC 296-874-30024: Use emergency escape and rescue devices appropriately.
Make sure devices whose sole function is to provide emergency escape and rescue aren’t used as working platforms.
Note: Systems which are designed to function both as suspended scaffolds and emergency systems may be used as working platforms.
WAC 296-874-30026: Protect suspension ropes from heat or corrosive substances
Shield suspension ropes from heat-producing processes.
Make sure, when acids or other corrosive substances are used on a scaffold, that the suspension ropes are protected by at least one of the following:
-
- Shielding
- Treating to protect the rope from the corrosive substances
- Making the rope of material that the corrosive substance won’t damage
WAC 296-874-30028: Take precautions while welding.
Do the following to protect employees while welding on suspended scaffolds:
-
- Use an insulated thimble to attach each suspension wire rope to its hanging support, such as a cornice hook or outrigger
- Insulate excess suspension wire rope and any additional independent lines to prevent grounding
- Cover the wire suspension rope with insulating material that extends at least 4 feet (1.2 m) above the hoist
- Make sure any tail line that extends below the hoist is:
- Insulated to prevent contact with the platform; and
- Guided or retained so it doesn’t become grounded.
- Cover each hoist with an insulated protective cover
- Connect the scaffold to the structure using a grounding conductor that:
- Is at least the size of the welding process work lead; and
- Isn’t in series with the welding process or the work piece.
- Shut off the welding machine if the scaffold grounding lead becomes disconnected
- Make sure an active welding rod or an uninsulated welding lead isn’t allowed to contact the:
- Scaffold; or
- Scaffold suspension system.
WAC 296-874-30030: Prohibit use of gasoline-powered equipment on suspended scaffolds.
Make sure gasoline-powered equipment is not used on suspended scaffolds.
WAC 296-874-30032: Meet these requirements when using catenary scaffolds:
Make sure catenary scaffolds have:
-
- No more than one platform between consecutive vertical pickups; and
- No more than 2 platforms per scaffold.
- Make sure any platform that’s supported by wire ropes has hook-shaped stops placed at each end of the platform that will prevent it from falling if one of the horizontal wire ropes breaks.
- Make sure wire ropes are:
- Continuous and without splices between anchors; and Not tightened to the point that putting a load on the scaffold will overstress them.
Reference: For specific fall protection requirements for employees on catenary scaffolds, go to WAC 296-874-20056.
- Continuous and without splices between anchors; and Not tightened to the point that putting a load on the scaffold will overstress them.
WAC 296-874-30036: Meet these requirements when using interior hung scaffolds:
Suspend the scaffold only from the roof structure or other structural member, such as ceiling beams.
Inspect the overhead supporting members and check to make sure they’re strong enough before erecting the scaffold.
Connect suspension ropes and cables to the overhead supporting members by:
-
- Shackles, clips, or thimbles; or
- Other means that meet equivalent criteria, such as strength and durability.
WAC 296-874-30038: Meet these requirements when using multi-level suspended scaffolds:
Equip scaffolds with additional independent support lines that meet all of the following:
-
- There are the same number of support lines as there are connection points for the suspension ropes
- The support lines are equivalent in strength to the suspension ropes
- The support lines are rigged to support the scaffold if the suspension ropes fail.
Make sure the independent support lines and the suspension ropes aren’t attached to the same points of anchorage.
Attach platform supports directly to the support stirrup and not to another platform
WAC 296-874-30040: Meet these requirements when using multi-point adjustable suspension scaffolds:
IMPORTANT: This requirement applies when using multi-point adjustable suspension scaffolds, stone setters’ multi-point adjustable suspension scaffolds, and masons’ multi-point adjustable suspension scaffolds.
Make sure masons’ multi-point adjustable suspension scaffold connections are designed by an engineer experienced in designing this type of scaffold.
Make sure bridges between 2 or more scaffolds meet all of the following:
-
- The scaffolds were designed to be bridged
- The bridges are articulated
- The hoists are properly sized.
Make sure passage from one platform to another, without using bridges, is done only when the platforms are:
-
- At the same height; and
- Abutting.
Suspend scaffolds from:
-
- Metal outriggers, brackets, wire rope slings, or hooks; or
- Other means that meet equivalent criteria, such as strength and durability.
WAC 296-874-30042: Meet these requirements when using needle beam scaffolds:
Install scaffold support beams on edge.
Use ropes or hangers for scaffold supports.
One end of a needle beam scaffold may be supported by a permanent structural member.
Securely attach ropes to the needle beams.
Arrange the support connection to prevent the needle beam from rolling or becoming displaced.
Securely attach platform units to the needle beams with bolts or equivalent means.
Note: Cleats and overhang aren’t adequate means of attachment.
Reference: For specific fall protection requirements for employees on needle beam scaffolds, go to WAC 296-874-20056.
WAC 296-874-30044: Meet these requirements when using single-point adjustable suspension scaffolds:
Make sure 2 scaffolds that have been combined to form a two-point adjustable suspension scaffold meet the requirements of the section, Make sure two-point adjustable suspension scaffolds (swing stages) meet these requirements, WAC 296-874- 30046.
Make sure scaffolds, where the suspension rope between the scaffold and the suspension device isn’t vertical, meet all of the following:
-
- The rigging has been designed by a qualified person
- The scaffold is accessible to rescuers
- The suspension rope is protected from chafing at any point where it changes direction
- The scaffold is positioned so that swinging can’t bring the scaffold into contact with another surface.
Make sure boatswains’ chair tackle meets of all of the following:
-
- It consists of correct size ball bearing blocks or bushed blocks
- The blocks contain safety hooks
- The rope is properly eye-spliced
- The rope is either:
- First-grade manila rope that has a diameter of at least 5/8 inch
(1.6 cm)
or - Other rope that has equivalent characteristics, such as strength and durability.
- First-grade manila rope that has a diameter of at least 5/8 inch
Make sure boatswain’s chair seat slings meet all of the following:
-
- Are reeved through 4 corner holes in the seat
- Cross each other on the underside of the seat
- Are rigged to prevent slipping which could cause the seat to become out-of-level
- Are made from fiber, synthetic, or other rope which have:
- A diameter of at least 5/8 inch (1.6 cm); and
- Characteristics equivalent to first grade manila rope, such as strength, slip resistance, and durability.
Make sure the seat sling of boatswain’s chairs used when a heat-producing process, such as gas or arc welding, is being conducted, is at least 3/8 inch (1.0 cm) wire rope.
Securely fasten cleats to the underside of noncross-laminated wood boatswain’s chairs to prevent the board from splitting.
Reference: For specific fall protection requirements for employees on single-point adjustable suspension scaffolds, go to WAC 296-874-20056.
WAC 296-874-30046: Meet these requirements when using two-point adjustable suspension scaffolds (swing stages):
IMPORTANT: This section doesn’t apply to two-point adjustable suspension scaffolds used as masons’ or stonesetters’ scaffolds.
Reference: For requirements for masons’ or stonesetters’ scaffolds, go to WAC 296- 874-30040
Make sure platforms more than 36 inches (0.9 m) wide have been designed by a qualified person to prevent unstable conditions.
Make sure platforms are one of the following:
-
- Ladder-type
- Plank-type
- Beam-type
- Light-metal type.
Make sure the design of light-metal type platforms have been tested and listed by a nationally recognized testing laboratory if they:
-
- Have a rated capacity of 750 lbs. or less; or
- Have a length of 40 feet (12.2 m) or less.
Securely fasten the platform to the hangers (stirrups) using U-bolts or other means that satisfy the section titled, Make sure suspended scaffolds and scaffold components meet these strength requirements, WAC 296-874-30002.
Make sure fiber or synthetic ropes are used with blocks that:
-
- Consist of at least one double and one single block; and
- Have sheaves that fit the size of the rope used.
Make sure employees move from one platform to another only when all of the following are met:
-
- The platforms are at the same height
- The platforms are abutting
- Walk-through stirrups are used that have been specifically designed to allow employee passage.
Make sure two-point scaffolds that are bridged or otherwise connected together when being raised or lowered meet both of the following:
-
- The bridge connections are articulated
-
- The hoists are properly sized.
Reference: For specific fall protection requirements for employees on two-point adjustable suspension scaffolds, go to WAC 296-874-20056.
WAC 296-874-40002: Supported scaffolds and scaffold components must meet strength requirements:
Make sure each supported scaffold and scaffold component can support, without failure, the total of its own weight plus at least 4 times the maximum intended load applied or transmitted to it.
WAC 296-874-40004: Prevent supported scaffolds from tipping
Make sure supported scaffolds with a height to least base dimension ratio of greater than 4 to one are prevented from tipping by one or more of the following:
-
- Guying
- Tying
- Bracing
- Other equivalent means.
Note: The least base dimension includes outriggers, if used.
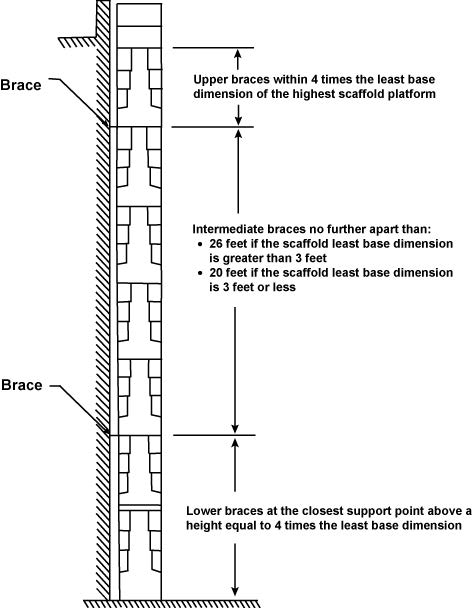
Install guys, ties, and braces where horizontal members support both the inner and outer legs of the scaffold.
Install guys, ties, and braces:
-
- According to the scaffold manufacturer’s recommendations; or
- At all points where the following horizontal and vertical planes meet:
- First vertical level at a height equal to 4 times the least base dimension
- Subsequent vertical levels every:
- 20 feet (6.1 m) or less for scaffolds having a width of 3 feet (0.91 m) or less
- 26 feet (7.9 m) or less for scaffolds more than 3 feet (0.91 m) wide
- Horizontally at:
- Each end of the scaffold; and
- Intervals of 30 feet (9.1 m) or less.
Note: The 30-foot horizontal intervals are measured from one end of the scaffold to the other.
Make sure the highest level of guys, ties, or braces is no further from the top of the scaffold than a distance equal to 4 times the least base dimension.
Make sure scaffolds that have an eccentric load applied or transmitted to them, such as a cantilevered work platform, are prevented from tipping by one or more of the following:
-
- Guying
- Tying
- Bracing
- Outriggers
- Other equivalent means.
WAC 296-874-40006: Supported scaffolds must be properly supported.
Make sure supported scaffold poles, legs, posts, frames, and uprights are:
-
- Plumb; and
- Braced to prevent swaying or displacement.
Make sure supported scaffold poles, legs, posts, frames, and uprights, bear on base plates that rest on:
-
- Mudsills; or
- Other firm foundations such as concrete or dry, compacted soil.
Make sure foundations are all of the following:
-
- Level
- Sound
- Rigid
- Capable of supporting the loaded scaffold without settling or displacement.
Note: The condition of the foundation may change due to weather or other factors. If changes occur, the foundation needs to be evaluated by a competent person to make sure it will safely support the scaffold.
Make sure unstable objects aren’t used:
-
- To support scaffolds or platform units; or
- As working platforms.
Make sure mobile scaffolds meet these additional requirements:
-
- Wheel and caster stems are pinned or otherwise secured in the scaffold legs or adjustment screws
- Wheels and casters are locked, or equivalent means are used, to prevent movement when the scaffold is being used
- Screw jacks or other equivalent means are used if it’s necessary to level the work platform.
Make sure front-end loaders and similar equipment used to support scaffold platforms have been specifically designed for such use by the manufacturer.
Reference: When forklifts or other powered industrial trucks are used for personal lifting on support scaffold platforms, follow the requirements found in Forklifts and Other Powered Industrial Trucks, Chapter 296-863 WAC.
WAC 296-874-40008: Provide safe access for persons erecting or dismantling supported scaffolds.
Provide a safe means of access for persons erecting or dismantling scaffolds if it is:
-
- Feasible; and
- Does not create a greater hazard.
Have a competent person determine the feasibility of providing safe access.
Make sure the determination is based on site conditions and the type of scaffold being erected or dismantled.
Install a hook-on or attachable ladder as soon as scaffold erection has progressed to a point where it can be safely installed and used.
Make sure cross braces on tubular welded frame scaffolds aren’t used to access or egress from the scaffold.
Make sure the frames of tubular welded frame scaffolds that are used as climbing devices meet all of the following:
-
- Create a usable ladder
- Provide good hand holds and foot space
- Have horizontal members that are all of the following:
- Parallel
- Level
- Spaced not more than 22 inches apart vertically
WAC 296-874-40010: Provide fall protection for persons erecting or dismantling supported scaffolds.
Have a competent person determine the feasibility of providing fall protection for persons erecting or dismantling supported scaffolds.
Provide fall protection if the installation and use of fall protection is:
-
- Feasible; and
- Does not create a greater hazard.
WAC 296-874-40012: Meet these requirements when moving mobile scaffolds:
Make sure, before a scaffold is moved, that employees on the scaffold are made aware of the move.
Apply manual force being used to move a scaffold:
-
- As close to the base as practicable; and
- Within 5 feet (1.5 m) of the supporting surface.
Make sure power systems used to propel mobile scaffolds have been designed for such use.
Make sure forklifts, trucks, similar motor vehicles, or add-on motors aren’t used to propel scaffolds unless the scaffold has been designed to be used with that type of propulsion system.
Stabilize scaffolds to prevent tipping when they’re being moved.
Make sure a scaffold isn’t moved with employees riding on it unless all of the following are met:
-
- The surface on which the scaffold is being moved is:
- Within 3 degrees of level; and
- Free of pits, holes, and obstructions
- The surface on which the scaffold is being moved is:
No employee is on any part of the scaffold which extends out beyond the wheels, casters, or other supports
Outrigger frames, when used, are installed on both sides of the scaffold
The power system, if used:
-
- Applies the propelling force directly to the wheels; and
- Produces a speed of one foot per second (.3 mps) or less
The height of the scaffold:
-
- Isn’t more than 2 times the least base dimension; or
- The scaffold is designed and constructed to meet or exceed nationally recognized stability test requirements, such as those listed in ANSI/SIA A92.5, Boom-Supported Elevating Work Platforms, and ANSI/SIA A92.6, Self-Propelled Elevating Work Platforms.
WAC 296-874-40014: Meet these requirements when using bricklayers’ square scaffolds (squares):
Reinforce wood scaffolds with gussets on both sides of each corner.
Make sure diagonal braces are installed:
-
- On all sides of each square
- Between squares on the front and back sides of the scaffold
- Extending from the bottom of each square to the top of the next square.
- Make sure scaffolds meet all of the following:
- Are no more than 3 tiers high
- Are constructed and arranged so that each square rests directly above another square
- The upper tiers:
- Stand on a continuous row of planks laid across the next lower tier; and
- Are nailed down or otherwise secured to prevent displacement.
WAC 296-874-40018: Meet these requirements when using fabricated frame scaffolds (tubular welded frame scaffolds):
Make sure scaffolds over 125 feet (38.0 m) high above their base plates are:
-
- Designed by a registered professional engineer; and
- Constructed and loaded as specified in the design.
Brace frames and panels using crossbraces, horizontal braces, diagonal braces, or a combination thereof to secure vertical members together laterally.
Make sure the length of the crossbraces will:
-
- Automatically square and align the vertical members; and
- Make the scaffold plumb, level, and square.
Secure all brace connections.
Join frames and panels together vertically by using one of the following:
-
- Coupling pins
- Stacking pins
- Equivalent means.
Use pins or other equivalent means to lock scaffold frames or panels together vertically where uplift may occur.
Make sure brackets used to support cantilevered loads are all of the following:
-
- Seated with side-brackets parallel to the frames and end-brackets at 90 degrees to the frames
- Not bent or twisted from these positions
- Used only to support persons.
Exemption: Brackets may be used to support cantilevered loads other than personnel if the scaffold has been:
-
- Designed for other loads by a qualified engineer; and
- Built to withstand the tipping forces caused by those loads.
- Leave existing platforms undisturbed until new end frames have been set in place and braced, then move the platforms to the next level.
WAC 296-874-40020: Meet these requirements when using integral prefabricated scaffold access frames:
Make sure integral prefabricated scaffold access frames meet all of the following:
-
- Have been specifically designed and constructed to be used as ladder rungs
- Have a rung length of at least 8 inches (20 cm)
- Have a maximum spacing between rungs of 16-3/4 inches (43 cm)
- Are uniformly spaced within each frame section
- Have rest platforms at least every 20 feet (6.1 m) on all supported scaffolds more than 24 feet (7.3 m) high.
Note: Non uniform rung spacing caused by joining end frames together is allowed, provided the resulting spacing doesn’t exceed 16-3/4 inches (43 cm).
Make sure, when panels with rungs that are less than 11-1/2 inches long are used as work platforms, that employees use either:
-
- A positioning device; or
- A personal fall arrest system.
Reference:
-
- For personal fall arrest system requirements in this chapter, go to WAC 296-874-20058.
- For construction activities, go to Fall Restraint and Fall Arrest, Part C-1, in Safety Standards for Construction Work, Chapter 296-155 WAC.
WAC 296-874-40022: Meet these requirements when using form scaffolds and carpenter’s bracket scaffolds:
Secure folding-type metal brackets that have been extended for use, with:
-
- Bolts; or
- Locking-type pins.
Make sure wooden bracket-form scaffolds are an integral part of the form panel.
Attach each bracket, other than those for wooden bracket-form scaffolds, to the supporting formwork or structure by using one or more of the following:
-
- Nails
- A metal stud attachment device
- Welding
- Hooking over a secured structural supporting member, with the form wales either:
- Bolted to the form; or
- Secured by snap ties or tie bolts extending through the form and securely anchored
- For carpenters’ bracket scaffolds only, using a bolt extending through to the opposite side of the structure’s wall.
WAC 296-874-40024: Meet these requirements when using horse scaffolds:
Make sure horse scaffolds aren’t constructed or arranged higher than 2 tiers or 10 ft. (3.0 m), whichever is less.
Do all of the following if horses are arranged in tiers:
-
- Place each horse directly over the horse in the tier below
- Nail down or otherwise secure the legs of each horse to prevent displacement
- Crossbrace each tier.
WAC 296-874-40026: Meet these requirements when using ladder jack scaffolds:
Make sure platform height isn’t higher than 20 feet (6.1 m).
Make sure ladder jacks are designed and constructed so they rest:
-
- On the side rails and ladder rungs together; or
- Only on the rungs.
Make sure ladder jacks that rest on rungs only have a bearing area that includes a length of at least 10 inches (25.4 cm) on each rung.
Make sure ladders used to support ladder jacks are:
-
- Type I (250 lbs. rated capacity) or Type IA (300 lbs. rated capacity); and
- Are placed, fastened, or equipped with devices to prevent slipping
Note: Ladders with a duty rating or weight capacity greater than a Type I ladder (250 lbs.) satisfy the requirement to use Type I or IA ladder.
Make sure job-made ladders aren’t used to support ladder jack scaffolds.
Make sure scaffold platforms aren’t bridged together.
Reference: There are specific fall protection requirements for employees using ladder jack scaffolds. Go to WAC 296-874-20056.
Requirements for portable and fixed ladders are found in chapter 296-876 WAC, Ladders, portable and fixed.
WAC 296-874-40028: Meet these requirements when using outrigger scaffolds:
Make sure outrigger scaffolds and scaffold components are:
-
- Designed by a registered professional engineer; and
- Constructed and loaded as specified in the design.
Make sure the part of the outrigger beam from the fulcrum point to the inboard end (farthest point of anchorage) is at least 1-1/2 times longer than the part from fulcrum point to the outboard end (the platform side).
Place I-beam or channel shaped outrigger beams so that the web section is vertical.
Make sure the fulcrum point of outrigger beams rests on secure bearings at least 6 inches (15.2 cm) in each horizontal dimension.
Make sure outrigger beams are:
-
- Secured in place to prevent movement; and
- Securely braced at the fulcrum point against tipping.
Securely anchor the inboard ends of outrigger beams by using one or both of the following:
-
- Braced struts bearing against sills that are in contact with the overhead beams or ceiling; or
- Tension members secured to the floor joists below.
Securely brace the entire supporting structure to prevent any horizontal movement.
Nail, bolt, or otherwise secure platform units to the outriggers to prevent platform displacement. Platform units must extend to within 3 inches of the building wall.
WAC 296-874-40030: Meet these requirements when using pole scaffolds:
Make sure pole scaffolds over 60 feet high are:
-
- Designed by a registered professional engineer; and
- Constructed and loaded as specified in the design.
Leave existing platforms undisturbed until new bearers have been set in place and braced before moving the platforms to the new level.
Install bracing on double-pole scaffolds as follows:
-
- Crossbracing between the inner and outer sets of poles
- Diagonal bracing in both directions across the entire outside face of the scaffold
- Diagonal bracing in both directions across the entire inside face of scaffolds that are used to support loads equivalent to a uniformly distributed load of 50 lbs. (222 kg) or more per square foot (929 sq. cm).
Install diagonal bracing on single pole scaffolds in both directions across the entire outside face of the scaffold.
Make sure runners meet all of the following:
-
- Are installed on edge
- Extend over a minimum of 2 poles
- Are supported by bearing blocks securely attached to the poles.
Make sure bearers are:
-
- Installed on edge; and
- Extend a minimum of 3 inches (7.6 cm) over the outside edges of runners.
Make sure runners, bearers, and braces aren’t spliced between poles.
Make sure wood poles that are spliced together meet both of the following:
-
- The ends of the poles at the splice:
- Are square; and
- The upper section rests squarely on the lower section
- Wood splice plates are provided that meet all of the following:
- Are installed on at least 2 adjacent sides
- Extend at least 2 feet (0.6 m) on either side of the splice
- Overlap the abutted ends equally
- Have the same cross-sectional areas as the pole.
- The ends of the poles at the splice:
Note: Splice plates of material other than wood may be used if they are of equivalent strength.
WAC 296-874-40032: Meet these requirements when using pump jack scaffolds:
Make sure pump jack brackets, braces, and accessories are made from metal plates and angles.
Make sure pump jack brackets have 2 positive gripping mechanisms to prevent any failure or slippage.
Secure poles to the structure using rigid triangular bracing or the equivalent located at all of the following:
-
- Top
- Bottom
- Other points on the pole as necessary.
Do both of the following when the pump jack has to pass bracing that’s already installed:
-
- Install an additional brace approximately 4 feet (1.2 m) above the brace to be passed
- Leave it in place until:
- The pump jack has been moved; and
- The original brace is reinstalled
Make sure work benches aren’t used as scaffold platforms.
Note: A work bench may be used as a toprail only if it meets the toprail requirements in, Make sure guardrail systems meet these requirements, WAC 296- 874-20064.
Make sure wood poles used with pump jack scaffolds are:
-
- Straight grained; and
- Free of shakes, large loose or dead knots, and other defects which might impair strength.
Make sure wood poles that are constructed of 2 continuous lengths are joined together with the seam parallel to the bracket.
Install a mending plate at all splices to develop the full strength of the member when splicing two-by-fours together to make a pole.
WAC 296-874-40034: Meet these requirements when using repair bracket scaffolds:
Make sure brackets are all of the following:
-
- Secured in place by at least one wire rope that’s at least 1/2 inch (1.27 cm) in diameter
- Attached to the securing wire rope by a positive locking device, or equivalent, that will prevent the bracket from being unintentionally detached from the rope
- Provided with a shoe, heel block, foot, or a combination that:
- Is located at the contact point between the supporting structure and the bottom of the bracket; and
- Will prevent lateral movement of the bracket
Secure the platforms to the brackets in a way that prevents:
-
-
- The platforms from separating from the brackets; and
- The platforms or brackets from moving on a completed scaffold.
-
Make sure wire rope placed around the structure to provide a safe anchorage for personal fall arrest systems used by employees erecting or dismantling scaffolds:
-
-
- Is at least 5/16 inch (0.8 cm) in diameter; and
- Provides an anchorage that meets the requirements of WAC 296-874-20058.
- For construction activities, go to Fall Restraint and Fall Arrest, Part C-1, in the Safety Standards for Construction Work, Chapter 296-155 WAC.
-
Make sure each wire rope used for securing brackets in place or as an anchorage for personal fall arrest systems is all of the following:
-
-
-
- Protected from damage due to contact with edges, corners, protrusions, or other parts of the supporting structure or scaffold components
- Tensioned by a turnbuckle or equivalent means. Turnbuckles must be:
- At least one inch (2.54 cm) in diameter; and
- Connected to the other end of its rope by an eye splice thimble that’s sized appropriate to the turnbuckle
- Not used with U-bolt wire rope clips.
-
-
Make sure materials aren’t dropped to the outside of the supporting structure.
Erect the scaffold by progressing around the structure in only one direction
WAC 296-874-40036: Meet these requirements when using roof bracket scaffolds:
Make sure scaffold brackets meet all of the following:
-
- Are constructed to fit the pitch of the roof
- Provide a level support for the platform
- Are anchored in place by nails.
Note: If it’s not practical to use nails to anchor brackets, secure them in place with first grade manila rope of at least 3/4 inch (1.9 cm) diameter, or equivalent.
WAC 296-874-40038: Meet these requirements when using step, platform and trestle ladder scaffolds:
Make sure ladders used to support step, platform, and trestle ladder scaffolds are:
-
- Type I (250 lb. rated capacity) or Type IA (300 lb. rated capacity); and
- Placed, fastened, or equipped with devices to prevent slipping.
Note: Ladders with a duty rating or weight capacity greater than a Type I ladder (250 lbs.) satisfy the requirements to use a Type I or Type IA ladder.
Make sure job-made ladders aren’t used to support step, platform, and trestle ladder scaffolds.
Reference:
-
- There are specific fall protection requirements for employees using ladder jack scaffolds. Go to WAC 296-874-20056.
- Requirements for portable and fixed ladders are found in chapter 296-876 WAC, Ladders, portable and fixed.
- Make sure scaffold platforms aren’t placed higher than the second highest rung or step of the ladder supporting the platform.
- Make sure scaffold platforms aren’t bridged together.
WAC 296-874-40040: Meet these requirements when using tube and coupler scaffolds:
Make sure tube and coupler scaffolds over 125 feet high are:
-
- Designed by a registered professional engineer; and
- Constructed and loaded as specified in the design.
Leave existing platforms undisturbed until new bearers have been set in place and braced before moving the platforms to the new level.
Install cross bracing across the width of the scaffold that meets all of the following:
-
- Bracing is installed at:
- Each end of the scaffold; and
- At least at every third set of posts horizontally and every fourth runner vertically.
- Bracing extends diagonally from the:
- Outer posts or runners upwards to the next inner posts or runners
and - Inner posts or runners upwards to the next outer posts or runners.
- Outer posts or runners upwards to the next inner posts or runners
- Bracing is installed at:
Install building ties:
-
- At the bearer levels between the cross bracing; and
- At locations specified in WAC 296-874-40004.
Install longitudinal bracing on straight run scaffolds as follows:
-
- Diagonally in both directions across the inner and outer rows of posts
- From the base of the end posts upward to the top of the scaffold at approximately a 45 degree angle
- As close as possible to the intersection of the bearer and post or runner and post
- If the scaffold is longer than it is tall, repeat the bracing beginning at every fifth post
- If the scaffold is taller that its length, install the bracing:
- From the base of the end posts upward to the opposite end posts;
and - In alternating directions until reaching the top of the scaffold.
- From the base of the end posts upward to the opposite end posts;
Attach bracing to the runners as close to the post as possible, if bracing can’t be attached to the post.
Make sure bearers meet all of the following:
-
- Are installed transversely between posts
- If the bearer is coupled to the post, have the inboard coupler bear directly on the runner coupler
- If the bearer is coupled to the runners, have the couplers as close to the posts as possible
- Extend bearers beyond the posts and runners
- Provide full contact with the coupler
- The bottom bearers are located as close to the base as possible.
Make sure runners meet all of the following:
-
- Are installed along the length of the scaffold
- Are located on both the inside and outside posts at the same height
- Are interlocked on straight runs to form continuous lengths and are coupled to each post
- The bottom runners are located as close to the base as possible.
Note: Tube and coupler guardrails and midrails installed on outside posts can be used in lieu of outside runners.
-
- Make sure couplers are made of a structural metal, such as drop-forged steel, malleable iron, or structural grade aluminum.
- Prohibit using couplers made of gray cast iron.
WAC 296-874-40042: Meet these requirements when using window jack scaffolds:
Make sure window jack scaffolds meet all of the following:
-
- Are securely attached to the window opening
- Are used for working only at the window opening the jack is placed through
- Aren’t used:
- To support planks placed between one window jack and another;
or - As any other element of scaffolding
- To support planks placed between one window jack and another;
WAC 296-874-500: Definitions
Adjustable suspension scaffold: A suspended scaffold equipped with one or more hoists that can be operated by employees on the scaffold
Bearer: A horizontal scaffold member (which may be supported by ledgers or runners) upon which the scaffold platform rests and which joins scaffold uprights, posts, poles, and similar members.
Boatswains’ chair: A single-point adjustable suspended scaffold consisting of a seat or sling designed to support one employee in a sitting position.
Brace: A rigid connection that holds one scaffold member in a fixed position with respect to another member, or to a building or structure.
Bricklayers’ square scaffold: A supported scaffold composed of framed squares which support a platform
Carpenters’ bracket scaffold: A supported scaffold consisting of a platform supported by brackets attached to building or structural walls.
Catenary scaffold: A suspended scaffold consisting of a platform supported by 2 essentially horizontal and parallel ropes attached to structural members of a building or other structure. Additional support may be provided by vertical pickups
Cleat: A structural block used at the end of a platform to prevent the platform from slipping off its supports. Cleats are also used to provide footing on sloped surfaces such as access ramps.
Competent person: Someone who – Is capable of identifying existing and predictable hazards in the surroundings or working conditions which are unsanitary, hazardous, or dangerous to employees and has the authority to take prompt corrective measures to eliminate them.
Coupler: A device for locking together the tubes of a tube and coupler scaffold.
Double-pole (independent pole) scaffold: A supported scaffold consisting of one or more platforms resting on cross beams (bearers) supported by ledgers and a double row of uprights independent of support (except ties, guys, braces) from any structure.
Equivalent: Alternative design, material or method to protect against a hazard. You have to demonstrate it provides an equal or greater degree of safety for employees than the method, material or design specified in the rule.
Exposed power lines: Electrical power lines which are accessible to and may be contacted by employees. Such lines don’t include extension cords or power tool cords.
Eye or eye splice: A loop at the end of a wire rope.
Fabricated frame scaffold (tubular welded frame scaffold): A scaffold consisting of platforms supported on fabricated frames with integral posts, horizontal bearers, and intermediate members.
Failure: Load refusal, breaking, or separation of component parts. Load refusal is the point where the ultimate strength is exceeded.
Float (ship) scaffold: A suspended scaffold consisting of a braced platform resting on 2 parallel bearers and hung from overhead supports by ropes of fixed length.
Form scaffold: A supported scaffold consisting of a platform supported by brackets attached to formwork.
Guard rail system: A vertical barrier, consisting of, but not limited to, top rails, mid rails, and posts, erected to prevent employees from falling off a scaffold platform or walkway.
Hand rails (ladder stands): A rail connected to a ladder stand running parallel to the slope and/or top step.
Hoist: A manual or power-operated mechanical device to raise or lower a suspended scaffold.
Horse scaffold: A supported scaffold consisting of a platform supported by construction horses (saw horses). Horse scaffolds constructed of metal are sometimes known as trestle scaffolds.
Independent pole scaffold: See double pole scaffold.
Interior hung scaffold: A suspended scaffold consisting of a platform suspended from the ceiling or roof structure by fixed length supports.
Ladder jack scaffold: A supported scaffold consisting of a platform resting on brackets attached to ladders.
Ladder stand: A mobile, fixed-size, self-supporting ladder consisting of a wide flat tread ladder in the form of stairs.
Landing: A platform at the end of a flight of stairs.
Large area scaffold: A pole scaffold, tube and coupler scaffold, system scaffold, or fabricated frame scaffold erected over substantially the entire work area. For example: A scaffold erected over the entire floor area of a room.
Lean-to scaffold: A supported scaffold which is kept erect by tilting it toward and resting it against a building or structure.
Ledger: See runner.
Lifeline: A component consisting of a flexible line that connects to an anchorage at one end to hang vertically (vertical lifeline), or that connects to anchorages at both ends to stretch horizontally (horizontal lifeline). It serves as a means for connecting other components of a personal fall arrest system to the anchorage.
Lower levels: Areas below the level where the employee is located and to which an employee can fall. Such areas include, but aren’t limited to, ground levels, floors, roofs, ramps, runways, excavations, pits, tanks, materials, water, and equipment.
Masons’ adjustable supported scaffold: See self-contained adjustable scaffold.
Masons’ multi-point adjustable suspension scaffold: A continuous run suspended scaffold designed and used for masonry operations.
Maximum intended load: The total load of all persons, equipment, tools, materials, transmitted loads, and other loads reasonably anticipated to be applied to a scaffold or scaffold component at any one time.
Midrail: A rail, approximately midway between the toprail of a guardrail system and the platform, and secured to the uprights erected along the exposed sides and ends of a platform.
Mobile scaffold: Supported scaffold mounted on casters or wheels.
Multi-level suspended scaffold: A two-point or multi-point adjustable suspension scaffold with a series of platforms at various levels resting on common stirrups.
Multi-point adjustable suspension scaffold: A suspended scaffold consisting of a platform(s) which is suspended by more than 2 ropes from overhead supports and equipped with means to raise and lower the platform to desired work levels.
Needle beam scaffold: A suspended scaffold which has a platform supported by 2 bearers(needle beams) suspended from overhead supports.
Outrigger: A structural member of a supported scaffold which increases the base width of a scaffold. This provides support for and increases the stability of the scaffold.
Outrigger beam (suspended and supported): The structural member of a suspended scaffold or outrigger scaffold which provides support for the scaffold by extending the scaffold point of attachment to a point out and away from the structure or building.
Outrigger scaffold: A supported scaffold consisting of a platform resting on outrigger beams which projects beyond the wall or face of the building or structure. The inboard ends of the outrigger beams are secured inside the building or structure.
Overhand bricklaying: The process of laying bricks and masonry so that the surface of the wall is on the opposite side of the wall from the mason, requiring the mason to lean over the wall to complete the work. It includes mason tending and electrical installation incorporated into the brick wall during the overhand bricklaying process.
Personal fall arrest system: A system used to arrest an employee’s fall. It consists of an anchorage, connectors, and body harness and may also include a lanyard, deceleration device, lifeline, or combinations of these.
Platform: A work surface used in scaffolds, elevated above lower levels. Platforms can be constructed using individual wood planks, fabricated planks, fabricated decks, and fabricated platforms.
Pole scaffold: See single-pole scaffold and double (independent) pole scaffold.
Pump jack scaffold: A supported scaffold consisting of a platform supported by vertical poles and movable support brackets.
Qualified Person: A person who has successfully demonstrated the ability to solve problems relating to the subject matter, work, or project, either by:
-
-
-
-
-
-
-
-
-
-
-
-
-
-
- Possession of a recognized degree, certificate, or professional standing or
- Extensive knowledge, training and experience.
-
-
-
-
-
-
-
-
-
-
-
-
-
Rated load: The manufacturer’s specified maximum load to be lifted by a hoist or to be applied to a scaffold or scaffold component.
Repair bracket scaffold: A supported scaffold consisting of a platform supported by brackets. The brackets are secured in place around the circumference or perimeter of a chimney, stack, tank or other supporting structure by one or more wire ropes placed around the supporting structure.
Roof bracket scaffold: A supported scaffold used on a sloped roof. It consists of a platform resting on angular-shaped supports so that the scaffold platform is level.
Runner (ledger): The lengthwise horizontal spacing or bracing member which may support the bearers.
Scaffold: A temporary elevated platform, including its supporting structure and anchorage points, used for supporting employees or materials.
Self-contained adjustable scaffold: A combination supported and suspended scaffold consisting of an adjustable platform mounted on an independent supporting frame, not a part of the object being worked on, which is equipped with a means to raise and lower the platform. Such systems include rolling roof rigs, rolling outrigger systems, and some masons’ adjustable supported scaffolds.
Shore scaffold: A supported scaffold which is placed against a building or structure and held in place with props.
Single-point adjustable suspension scaffold: A suspended scaffold consisting of a platform suspended by one rope from an overhead support and equipped with means to permit the movement of the platform to desired work levels.
Single-pole scaffold: A supported scaffold consisting of platforms resting on bearers, the outside ends of which are supported on runners secured to a single row of posts or uprights, and the inner ends of which are supported on or in a structure or building wall.
Stair tower (scaffold stairway/tower): A tower comprised of scaffold components which contain internal stairway units and rest platforms. These towers are used to provide access to scaffold platforms and other elevated points such as floors and roofs.
Stall load: The load at which the prime mover of a power-operated hoist stalls or the power to the prime mover is automatically disconnected.
Step, platform, and trestle ladder scaffold: A platform resting directly on the rungs of a step, platform, or trestle ladder.
Stilts: A pair of poles or similar supports with raised footrests, used to permit walking above the ground or working surface.
Stonesetters’ multi-point adjustable suspension scaffold: A continuous run suspended scaffold designed and used for stonesetters’ operations.
Supported scaffold: One or more platforms supported by rigid means such as outrigger beams, brackets, poles, legs, uprights, posts, or frames.
Suspended scaffold: One or more platforms suspended from an overhead structure by ropes or other non-rigid means.
System scaffold: A scaffold consisting of posts with fixed connection points that accept runners, bearers, and diagonals that can be interconnected at predetermined levels.
Toe board (scaffold): A barrier erected along the exposed sides and ends of a scaffold platform at platform level to prevent material, tools, and other loose objects from falling from the platform.
Top plate bracket scaffold: A scaffold supported by brackets that hook over or are attached to the top of a wall. This type of scaffold is similar to carpenters’ bracket scaffolds and form scaffolds.
Tube and coupler scaffold: A scaffold consisting of platforms supported by tubing, erected with coupling devices connecting uprights, braces, bearers, and runners.
Tubular welded frame scaffold: See fabricated frame scaffold. Tubular welded sectional folding scaffold: A sectional, folding metal scaffold either of ladder frame or inside stairway design. It’s substantially built of prefabricated welded sections, which consist of end frames, platform frame, inside inclined stairway frame and braces, or hinged connected diagonal and horizontal braces. It can be folded into a flat package when the scaffold isn’t in use.
Two-point suspension scaffold (swing stage): A suspended scaffold consisting of a platform supported by hangers (stirrups), suspended by 2 ropes from overhead supports, and equipped with means to permit the raising and lowering of the platform to desired work levels.
Unstable objects: Items whose strength, configuration, or lack of stability may allow them to become dislocated and shift and therefore may not properly support the loads imposed on them. Unstable objects don’t constitute a safe base support for scaffolds, platforms, or employees. Examples include, but aren’t limited to, barrels, boxes, loose brick, and concrete blocks.
Vertical pickup: A rope used to support the horizontal rope in a catenary scaffold.
Walkway (scaffold): Part of a scaffold used only for access and not as a working level.
Window jack scaffold: A platform resting on a bracket or jack that projects through a window opening.
Work level: The elevated platform, used for supporting workers and their materials.